What is Porosity in Welding: Important Tips for Getting Flawless Welds
What is Porosity in Welding: Important Tips for Getting Flawless Welds
Blog Article
Porosity in Welding: Identifying Common Issues and Implementing Ideal Practices for Prevention
Porosity in welding is a pervasive problem that commonly goes undetected up until it causes significant troubles with the honesty of welds. This typical defect can jeopardize the stamina and sturdiness of bonded structures, posing safety and security threats and bring about pricey rework. By comprehending the origin of porosity and implementing effective avoidance methods, welders can significantly boost the high quality and dependability of their welds. In this discussion, we will explore the key factors adding to porosity formation, examine its harmful effects on weld efficiency, and talk about the most effective practices that can be embraced to reduce porosity incident in welding processes.
Usual Root Causes Of Porosity
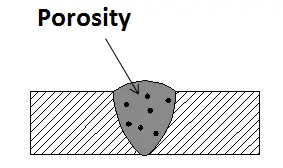
Utilizing filthy or damp filler products can present pollutants right into the weld, contributing to porosity problems. To alleviate these common causes of porosity, detailed cleaning of base metals, correct protecting gas option, and adherence to optimal welding criteria are essential techniques in attaining high-grade, porosity-free welds.
Impact of Porosity on Weld Top Quality

The visibility of porosity in welding can significantly endanger the architectural honesty and mechanical properties of bonded joints. Porosity develops voids within the weld metal, deteriorating its total toughness and load-bearing ability. These gaps act as stress and anxiety concentration points, making the weld extra vulnerable to cracking and failure under applied lots. Additionally, porosity can reduce the weld's resistance to rust and various other ecological factors, further decreasing its longevity and performance.
Welds with high porosity levels often tend to show lower influence toughness and reduced capacity to deform plastically before fracturing. Porosity can hinder the weld's capacity to effectively transmit pressures, leading to early weld failure and prospective security check over here threats in vital structures.
Best Practices for Porosity Avoidance
To boost the architectural integrity and quality of welded joints, what certain steps can be executed to minimize the incident of porosity throughout the welding procedure? Using the proper welding technique for the certain product being welded, such as readjusting the welding angle and weapon placement, can further stop porosity. Normal inspection of welds and instant removal of any concerns identified throughout the welding procedure are essential practices to prevent porosity and produce top quality welds.
Importance of Correct Welding Methods
Executing correct welding techniques is critical in making certain the structural honesty and quality of bonded joints, building upon the structure of efficient porosity prevention steps. Welding methods directly impact the overall toughness and longevity of the welded framework. One vital facet of correct welding strategies is preserving the right warm input. Extreme heat can result in boosted porosity as a result of the entrapment of gases in the weld swimming pool. Conversely, insufficient warmth might lead to incomplete blend, creating prospective weak points in the joint. Furthermore, using the suitable welding parameters, such as voltage, present, and take a trip speed, is important for accomplishing audio welds with marginal porosity.
Moreover, the option check these guys out of welding process, whether it be MIG, TIG, or stick welding, should line up with the certain requirements of the job to make sure ideal outcomes. Correct cleansing and preparation of the base metal, in addition to picking the right filler material, are likewise essential parts of skilled welding strategies. By adhering to these best methods, welders can lessen the danger of porosity formation and generate premium, structurally audio welds.

Examining and Quality Assurance Procedures
Evaluating procedures are vital to find and protect against porosity in welding, guaranteeing the toughness and longevity of the last product. Non-destructive screening approaches such as ultrasonic testing, radiographic screening, and click for more info aesthetic examination are typically used to identify potential flaws like porosity.
Post-weld examinations, on the various other hand, examine the final weld for any kind of flaws, including porosity, and validate that it meets specified requirements. Implementing a comprehensive quality control plan that consists of detailed screening procedures and examinations is vital to decreasing porosity issues and guaranteeing the overall top quality of bonded joints.
Final Thought
Finally, porosity in welding can be an usual problem that influences the quality of welds. By determining the common reasons for porosity and applying best methods for prevention, such as appropriate welding methods and screening steps, welders can make sure top quality and reputable welds. It is essential to prioritize prevention techniques to minimize the incident of porosity and keep the honesty of bonded structures.
Report this page